Dairy Processing
21 Pasteurization
The process of pasteurization was named after Louis Pasteur who discovered that spoilage organisms could be inactivated in wine by applying heat at temperatures below its boiling point. The process was later applied to milk and remains the most important operation in the processing of milk.
Definition:
The heating of every particle of milk or milk product to a specific temperature for a specified period of time without allowing recontamination of that milk or milk product during the heat treatment process.
Purpose There are two distinct purposes for the process of milk pasteurization:
-
- Public Health Aspect – to make milk and milk products safe for human consumption by destroying all bacteria that may be harmful to health (pathogens)
- Keeping Quality Aspect – to improve the keeping quality of milk and milk products. Pasteurization can destroy some undesirable enzymes and many spoilage bacteria. Shelf life can be 7, 10, 14 or up to 16 days.
The extent of microorganism inactivation depends on the combination of temperature and holding time. Minimum temperature and time requirements for milk pasteurization are based on thermal death time studies for the most heat resistant pathogen found in milk, Coxelliae burnettii. Thermal lethality determinations require the applications of microbiology to appropriate processing determinations. An overview can be found on the next page.
To ensure destruction of all pathogenic microorganisms, time and temperature combinations of the pasteurization process are highly regulated:
Ontario Pasteurization Regulations
Milk:
63° C for not less than 30 min.,
72° C for not less than 16 sec.,
or equivalent destruction of pathogens and the enzyme phosphatase as permitted by Ontario Provincial Government authorities. Milk is deemed pasteurized if it tests negative for alkaline phosphatase.
Frozen dairy dessert mix (ice cream or ice milk, egg nog):
at least 69° C for not less than 30 min;
at least 80° C for not less than 25 sec;
other time temperature combinations must be approved (e.g. 83° C/16 sec).
Milk based products– with 10% mf or higher, or added sugar (cream, chocolate milk, etc)
66° C/30 min, 75° C/16 sec
There has also been some progress with low temperature pasteurization methods using membrane processing technology.
Thermal Destruction of Microorganisms
Heat is lethal to microorganisms, but each species has its own particular heat tolerance. During a thermal destruction process, such as pasteurization, the rate of destruction is logarithmic, as is their rate of growth. Thus bacteria subjected to heat are killed at a rate that is proportional to the number of organisms present. The process is dependent both on the temperature of exposure and the time required at this temperature to accomplish to desired rate of destruction. Thermal calculations thus involve the need for knowledge of the concentration of microorganisms to be destroyed, the acceptable concentration of microorganisms that can remain behind (spoilage organisms, for example, but not pathogens), the thermal resistance of the target microorganisms (the most heat tolerant ones), and the temperature time relationship required for destruction of the target organisms.
The extent of the pasteurization treatment required is determined by the heat resistance of the most heat-resistant enzyme or microorganism in the food. For example, milk pasteurization historically was based on Mycobacterium tuberculosis and Coxiella burnetti, but with the recognition of each new pathogen, the required time temperature relationships are continuously being examined.A thermal death curve for this process is shown below. It is a logarithmic process, meaning that in a given time interval and at a given temperature, the same percentage of the bacterial population will be destroyed regardless of the population present. For example, if the time required to destroy one log cycle or 90% is known, and the desired thermal reduction has been decided (for example, 12 log cycles), then the time required can be calculated. If the number of microorganisms in the food increases, the heating time required to process the product will also be increased to bring the population down to an acceptable level. The heat process for pasteurization is usually based on a 12 D concept, or a 12 log cycle reduction in the numbers of this organism.
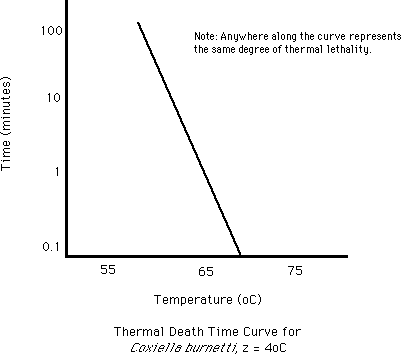
Several parameters help us to do thermal calculations and define the rate of thermal lethality. The D value is a measure of the heat resistance of a microorganism. It is the time in minutes at a given temperature required to destroy 1 log cycle (90%) of the target microorganism. (Of course, in an actual process, all others that are less heat tolerant are destroyed to a greater extent). For example, a D value at 72°C of 1 minute means that for each minute of processing at 72°C the bacteria population of the target microorganism will be reduced by 90%. In the illustration below, the D value is 14 minutes (40-26) and would be representative of a process at 72°C.
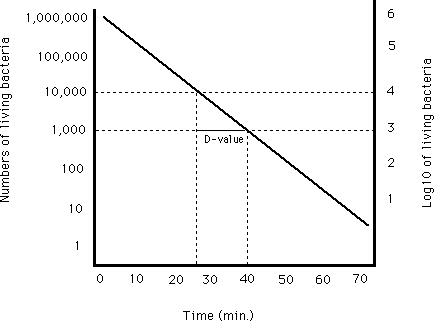
The Z value reflects the temperature dependence of the reaction. It is defined as the temperature change required to change the D value by a factor of 10. In the illustration below the Z value is 10°C.
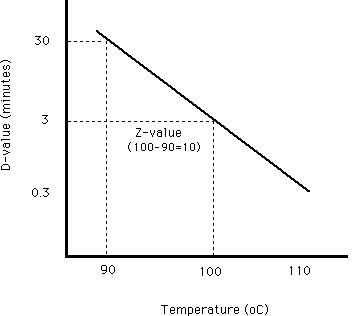
Reactions that have small Z values are highly temperature dependent, whereas those with large Z values require larger changes in temperature to reduce the time. A Z value of 10°C is typical for a spore forming bacterium. Heat induced chemical changes have much larger Z values that microorganisms, as shown below.
Bacteria Z (°C) 5-10 D121 (min) 1-5
enzymes Z (°C) 30-40 D121 (min) 1-5
vitamins Z (°C) 20-25 D121 (min) 150-200
pigments Z (°C) 40-70 D121 (min) 15-50
The figure below (which is schematic and not to scale) illustrates the relative changes in time temperature profiles for the destruction of microorganisms. Above and to the right of each line the microorganisms or quality factors would be destroyed, whereas below and to the left of each line, the microorganisms or quality factors would not be destroyed. Due to the differences in Z values, it is apparent that at higher temperatures for shorter times, a region exists (shaded area) where pathogens can be destroyed while vitamins can be maintained. The same holds true for other quality factors such as colour and flavour components. Thus in UHT milk processing, very high temperatures for very short times (e.g., 140oC for 1-2 s) are favoured compared to a lower temperature longer time processes since it results in bacterial spore elimination with a lower loss of vitamins and better sensory quality.
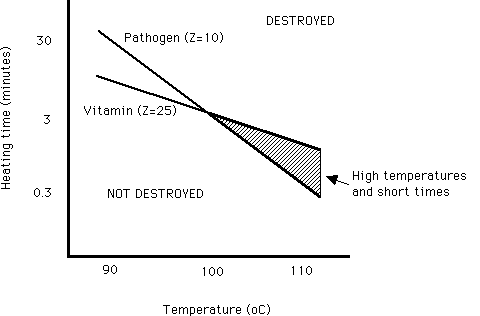
Alkaline phosphatase is a naturally-occurring enzyme in raw milk which has a similar Z value to heat-resistant pathogens. Since the direct estimation of pathogen numbers by microbial methods is expensive and time consuming, a simple test for phosphatase activity is routinely used. If activity is found, it is assumed that either the heat treatment was inadequate or that unpasteurized milk has contaminated the pasteurized product.
A working example of how to use D and Z values in pasteurization calculations:
Pooled raw milk at the processing plant has bacterial population of 4x10exp5/mL. It is to be processed at 79°C for 21 seconds. The average D value at 65°C for the mixed population is 7 min. The Z value is 7°C. How many organisms will be left after pasteurization? What time would be required at 65°C to accomplish the same degree of lethality?
Answer:
At 79°C, the D value has been reduced by two log cycles from that at 65°C since the Z value is 7°C. Hence it is now 0.07 min. The milk is processed for 21/60=0.35 min, so that would accomplish 5 log cycle reductions to 4 organisms/mL. At 65°C, you would need 35 minutes to accomplish a 5D reduction.
Methods of Pasteurization
Batch method
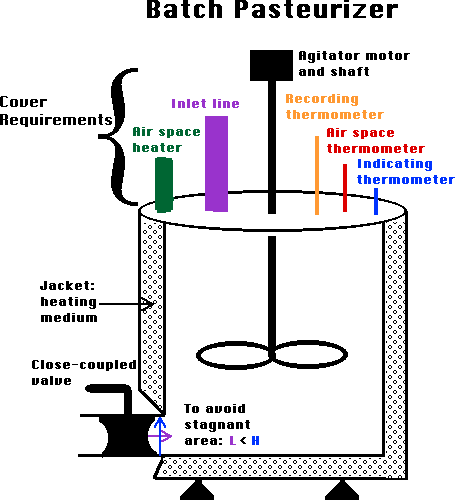
In the vat the milk is heated and held throughout the holding period while being agitated. The milk may be cooled in the vat or removed hot after the holding time is completed for every particle. As a modification, the milk may be partially heated in tubular or plate heater before entering the vat. This method has very little use for milk but some use for milk by-products (e.g. creams, chocolate) and special batches. The vat pasteurizer is used extensively in the ice cream industry as it allows for dissolution and blending of ingredients during the heating stage.
Continuous Method
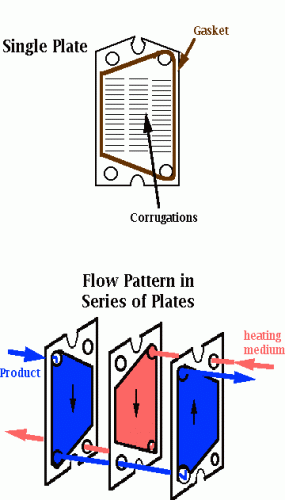
HTST Milk Flow Overview
Cold raw milk at 4° C in a constant level tank is drawn into the regenerator section of pasteurizer. Here it is warmed to approximately 57° C – 68° C by heat given up by hot pasteurized milk flowing in a counter current direction on the opposite side of thin, stainless steel plates. The raw milk, still under suction, passes through a positive displacement timing pump which delivers it under positive pressure through the rest of the HTST system.
The raw milk is forced through the heater section where hot water on opposite sides of the plates heat milk to a temperature of at least 72° C. The milk, at pasteurization temperature and under pressure, flows through the holding tube where it is held for at least 16 sec. The maximum velocity is governed by the speed of the timing pump, diameter and length of the holding tube, and surface friction. After passing temperature sensors of an indicating thermometer and a recorder-controller at the end of the holding tube, milk passes into the flow diversion device (FDD). The FDD assumes a forward-flow position if the milk passes the recorder-controller at the preset cut-in temperature (>72° C). The FDD remains in normal position which is in diverted-flow if milk has not achieved preset cut-in temperature. The improperly heated milk flows through the diverted flow line of the FDD back to the raw milk constant level tank. Properly heated milk flows through the forward flow part of the FDD to the pasteurized milk regenerator section where it gives up heat to the raw product and in turn is cooled to approximately 32° C – 9° C.
The warm milk passes through the cooling section where it is cooled to 4° C or below by coolant on the opposite sides of the thin, stainless steel plates. The cold, pasteurized milk passes through a vacuum breaker at least 12 inches above the highest raw milk in the HTST system then on to a storage tank filler for packaging.
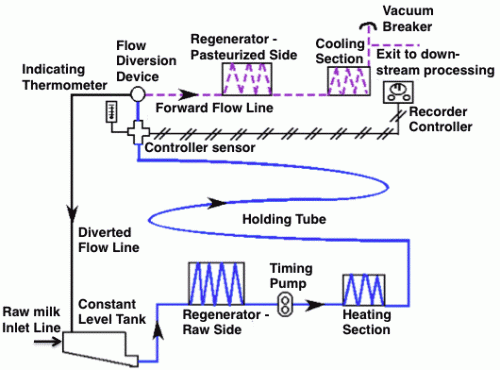
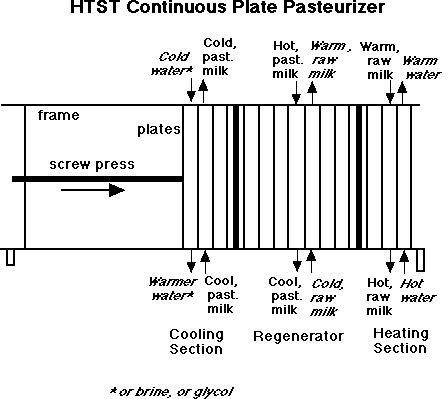
The diagram below illustrates HTST milk pasteurization equipment and flow diagram when incorporating a centrifugal booster pump (to help fill the regenerator on large systems) and pressure differential switch/back pressure controller on the regenerator (to maintain the pressure differential due to the action of the booster pump on the raw side). It also shows the position of the homogenizer when included in-line in the HTST system.
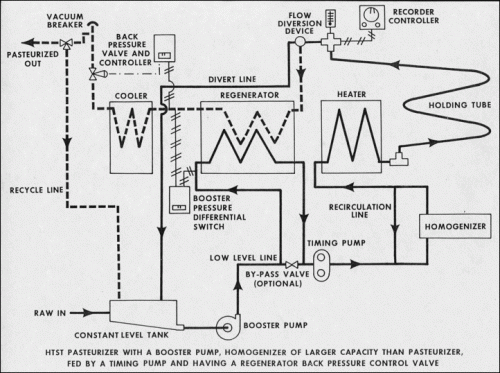
Holding Time
Re < 2100 laminar
Re > 4000 fully developed turbulent flow
There is an impact of these flow patterns on holding time calculations and the assessment of proper holding tube lengths.
The holding time is determined by timing the interval for an added trace substance (salt) to pass through the holder. The time interval of the fastest particle of milk is desired. Thus the results found with water are converted to the milk flow time by formulation since a pump may not deliver the same amount of milk as it does water.
Note: the formulation assumes flow patterns are the same for milk and water. If they are not, how would this affect the efficiency of the pasteurization process?
Pressure Differential
- The balance tank overflow level must be less than the level of lowest milk passage in the regenerator
- Properly installed booster pump is all that is permitted between balance tank and raw regenerator
- No pump after pasteurized milk outlet to vacuum breaker
- There must be greater than a 12 inch vertical rise to the vacuum breaker
- The raw regenerator drains freely to balance tank at shut-down
Basic Component Equipment of HTST Pasteurizer
Balance Tank
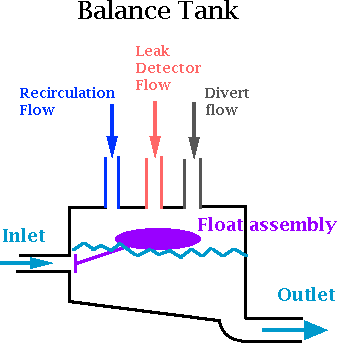
Regenerator
% regeneration = temp. increase due to regenerator/total temp. increase
For example: Cold milk entering system at 4° C, after regeneration at 65° C, and final temperature of 72° C would have an 89.7% regeneration:
65 – 4
______ = 89.7
72 – 4
Timing pump
Holding tube
Indicating thermometer
Recorder-controller (STLR)
Flow Diversion Device (FDD)
single stem – an older valve system that has the disadvantage that it can’t be cleaned in place.
dual stem – consists of 2 valves in series for additional fail safe systems. This FDD can be cleaned in place and is more suited for automation.
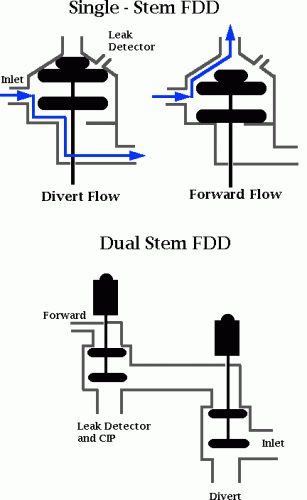
Vacuum Breaker
Auxiliary Equipment
Booster Pump
It is centrifugal “stuffing” pump which supplies raw milk to the raw regenerator for the balance tank. It must be used in conjunction with pressure differential controlling device and shall operate only when timing pump is operating, proper pressures are achieved in regenerator, and system is in forward flow.
Homogenizer
The homogenizer may be used as timing pump. It is a positive pressure pump; if not, then it cannot supplement flow. Free circulation from outlet to inlet is required and the speed of the homogenizer must be greater than the rate of flow of the timing pump.
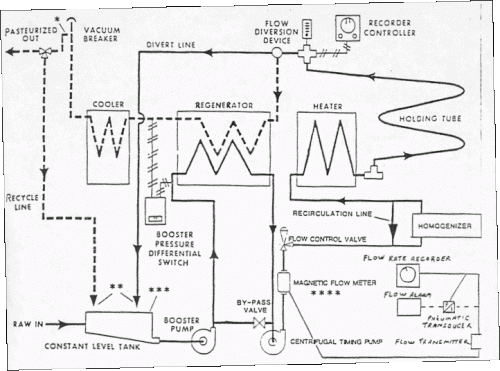
Magnetic flow meter and centrifugal pump arrangements
Magnetic flow meters (shown on the right) can be used to measure the flow rate. It is essentially a short piece of tubing (approximately 25 cm long) surrounded by a housing, inside of which are located coils that generate a magnetic field. When milk passes through the magnetic field, it causes a voltage to be induced, and the generated signal is directly proportional to velocity. Application of the magnetic flow meter in the dairy industry has centered around its replacing the positive displacement timing pump as the metering device in HTST pasteurizing systems, where with certain products the timing pump rotors reportedly wear out in a relatively short period of time. In operation, the electrical signal is sent by the magnetic flow meter to the flow controller, which determines what the actual flow is compared to the flow rate set by the operator. Since the magnetic flow meter continuously senses flow rate, it will signal the electronic controller if the actual flow exceeds the set flow rate for any reason. If the flow rate is exceeded for any reason, the flow diversion device is put into diverted flow. A significant difference from the normal HTST system (with timing pump) comes into focus at this point. This system can be operated at a flow rate greater than (residence time less than) the legal limit. However, it will be in diverted flow and never in forward flow.
Another magnetic flow meter based system with an AC variable frequency motor control drive on a centrifugal pump is also possible in lieu of a positive displacement metering pump on a HTST pasteurizer. This system does not use a control valve but rather the signal from the magnetic flow meter is transmitted to the AC variable frequency control to vary the speed of the centrifugal pump. The pump, then controls the flow rate of product through the system and its holding time in the holding tube.
Automated Public Health Controllers
This gives rise to a need for specific regulations or computer controlled CCP’s of public health significance:
- dedicated computer – no other assignments, monitor all CCP’s at least once/sec
- not under control of any other computer system or override system, i.e., network
- separate computer on each pasteurizer
- I/O bus for outputs only, to other computers no inputs from other computers
- on loss of power – public health computers should revert to fail safe position (e.g. divert)
- last state switches during power up must be fail safe position
- programs in ROM – tapes/disks not acceptable
- inputs must be sealed, modem must be sealed, program sealed
- no operator override switches
- proper calibration procedure during that printing – Public health computer must not leave public health control for > 1 sec and upon return must complete 1 full cycle before returning to printing
- FDV position must be monitored and temperature in holding tube recorded during change in FDV position
- download from ROM to RAM upon startup
- integrated with CIP computer which can be programmed e.g., FDV, booster pump controllable by CIP computer when in CIP made only