8.2 Manufacturing Process
Every organization—whether it produces goods or provides services— sees job #1 as providing customers with quality products. Thus, to compete with other organizations, a company must convert resources (materials, labour, money, information) into goods or services as efficiently as possible. The upper-level manager who directs this transformation process is called an operations manager. The job of operations management (OM) consists of all the activities involved in transforming a product idea into a finished product. Hence, because of the complexity of organizing all the activities in an organization, it is more important than ever for Operations Management to ensure due diligence is utilized to structure operations. Due diligence is the important actions taken by directors or managers of an organization to ensure that all potential risks and errors are mitigated entirely. In addition, operations managers are involved in planning and controlling the systems that produce goods and services. In other words, operations managers manage the process that transforms inputs into outputs. Figure 8.1 below illustrates these traditional functions of operations management.
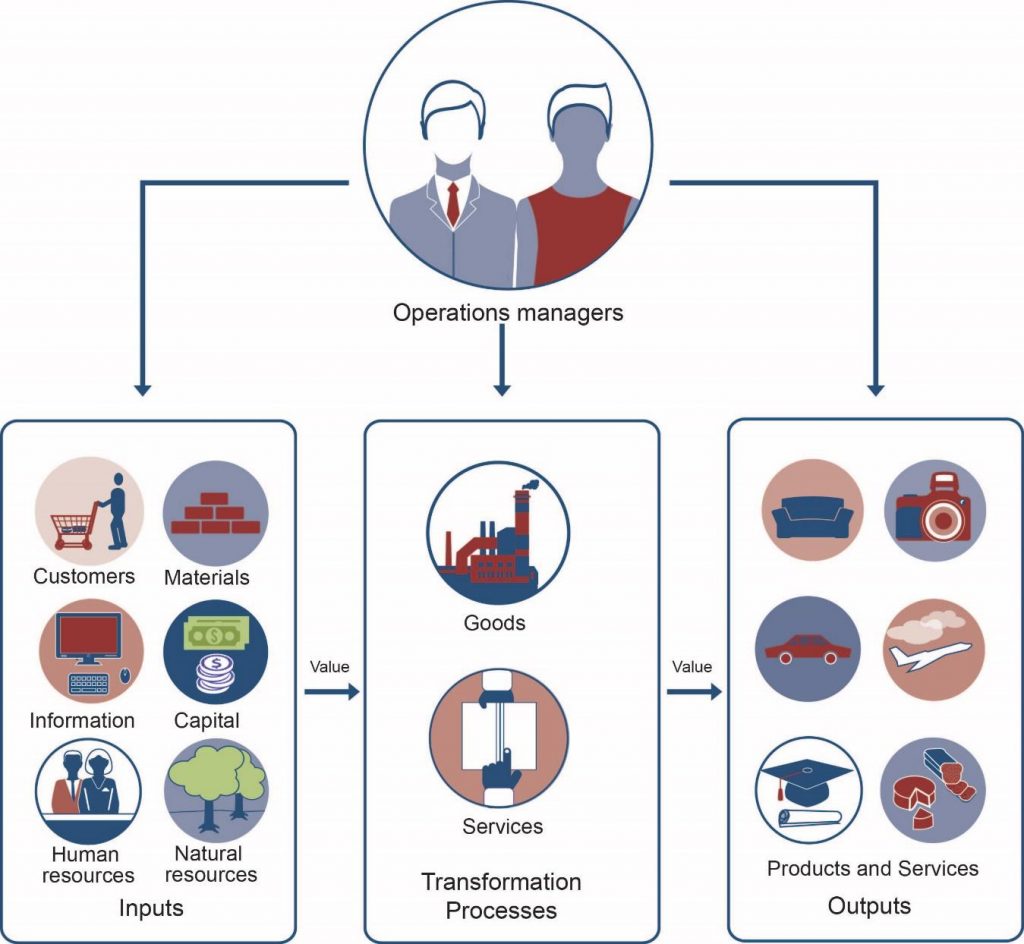
All manufacturers set out to perform the same basic function: to transform resources into finished goods. To perform this function in today’s business environment, manufacturers must continually strive to improve operational efficiency. They must fine-tune their production processes to focus on quality, to hold down the costs of materials and labour, and to eliminate all costs that add no value to the finished product.