Ice Cream Manufacture
4 Pasteurization of Mix
The mix is then pasteurized. Pasteurization is the biological control point in the system, designed for the destruction of pathogenic bacteria. In addition to this very important function, pasteurization also reduces the number of spoilage organisms such as psychrotrophs, and helps to hydrate some of the components (proteins, stabilizers).
Pasteurization (Ontario regulations): 69° C/30 min. 80° C/25s
Both batch pasteurizers and continuous (HTST) methods are used.
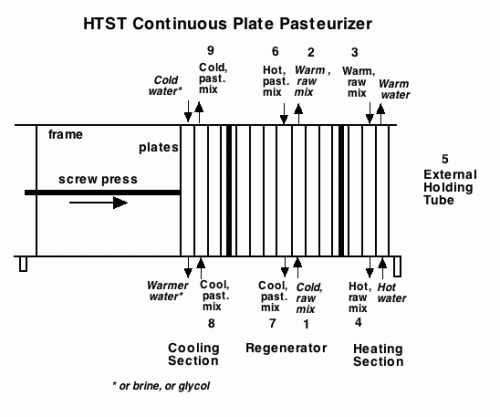
Batch pasteurizers lead to more whey protein denaturation, which some people feel gives a better body to the ice cream. In a batch pasteurization system, blending of the proper ingredient amounts is done in large jacketed vats equipped with some means of heating, usually steam or hot water. The product is then heated in the vat to at least 69 C (155 F) and held for 30 minutes to satisfy legal requirements for pasteurization, necessary for the destruction of pathogenic bacteria. Various time temperature combinations can be used. The heat treatment must be severe enough to ensure destruction of pathogens and to reduce the bacterial count to a maximum of 100,000 per gram. Following pasteurization, the mix is homogenized by means of high pressures and then is passed across some type of heat exchanger (plate or double or triple tube) for the purpose of cooling the mix to refrigerated temperatures (4 C). Batch tanks are usually operated in tandem so that one is holding while the other is being prepared. Automatic timers and valves ensure the proper holding time has been met.
Continuous pasteurization (see schematic diagram for mix to the right) is usually performed in a high temperature short time (HTST) heat exchanger following blending of ingredients in a large, insulated feed tank. Some preheating, to 30 to 40 C, is necessary for solubilization of the components. The HTST system is equipped with a heating section, a cooling section, and a regeneration section. Cooling sections of ice cream mix HTST presses are usually larger than milk HTST presses. Due to the preheating of the mix, regeneration is lost and mix entering the cooling section is still quite warm.